The core of PVC processing: a comprehensive analysis of 6 common auxiliary stabilizers
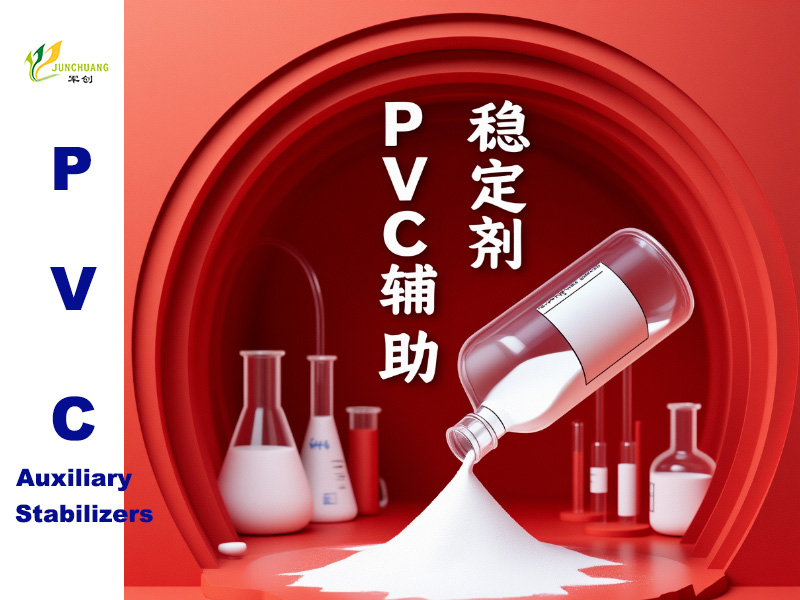
I. Phosphite: a powerful partner of calcium-zinc system Phosphite is an indispensable component of calcium-zinc compound stabilizers, and is usually added to liquid stabilizers at a ratio of 10% – 35%. It has a number of important functions: it can capture hydrogen chloride and effectively inhibit the degradation of PVC. Addition of polyolefins to enhance system stability. It has a plasticizing effect, but is not suitable for rigid PVC.
Currently, hydrolyzed diisooctyl benzene phosphite is more widely used, it can significantly improve the coloring, transparency and weatherability of products.
Second, epoxy compounds: light stabilization of the natural choice of epoxy soybean oil is the traditional auxiliary stabilizer of epoxy compounds, in recent years, some new epoxy resins have also shown high stability performance. The mechanism of action is as follows: Reaction with HCl generates chloroethanol, which replaces the unstable chlorine atoms in PVC. When used alone, the stabilizing effect is poor, but when used in combination with phosphite, the stabilizing effect is greatly improved.
These stabilizers are suitable for soft PVC products, especially those exposed to sunlight, but have the disadvantage of leaching.
Third, polyol: synergistic multi-faceted polyalcohol auxiliary stabilizers, such as pentaerythritol, sorbitol, etc., and β – diketone, epoxy compounds when used in conjunction with the excellent synergistic effect. Its mechanism of action includes: chelating metal ions, preventing chloride-catalyzed degradation. Displacing allyl chloride to extend the heat stabilization time of PVC. Forming complexes with metal soaps to inhibit “zinc burning”.
However, some polyols have the problem of easy sublimation, and esterification-modified polyols can effectively improve this situation.
Fourth, β – diketone: coloring control experts β – diketone is an essential auxiliary stabilizer in the calcium-zinc system, the amount of its addition is generally Ca / Zn composite stabilizer of 8% – 12%. Its main functions are: improve the initial coloring performance of products, inhibit the “zinc burning” phenomenon. Complexation with zinc salt to generate β – diketone zinc, accelerate the replacement of allyl chloride reaction.
Stearoyl benzoylmethane and dibenzoylmethane are the more widely used varieties, of which stearoyl benzoylmethane has also obtained FDA approval and can be used in food packaging materials.
V. Aminocrotonate and α-phenylindole: Special system synergists Aminocrotonate is generally thermally stable when used alone, and is usually used in conjunction with Ca/Zn composite stabilizers and epoxy compounds, which significantly improves the thermal stability of the system. α-phenylindole can significantly improve the performance of the system when used in conjunction with the Ca/Zn system in suspension PVC, but the coloring is poor at the initial stage, and is only applicable to alkali stabilized emulsion PVC. However, the initial colorability is poor, and it is only suitable for emulsion PVC stabilized by adding alkali.
Six, talc: green new hope talc-like layered double hydroxyl composite metal hydroxide (LDH) is a non-toxic auxiliary heat stabilizer with broad prospects. It has the following advantages: heat stabilization is better than barium soap, calcium soap and its mixtures. It has good transparency, insulation, weather resistance and processability. It can synergize with zinc soap and organotin heat stabilizers.
Its thermal stabilization is mainly realized through the absorption of HCl gas released by thermal decomposition of PVC by surface hydroxyl groups, or the exchange of HCl and interlayer CO3²-.