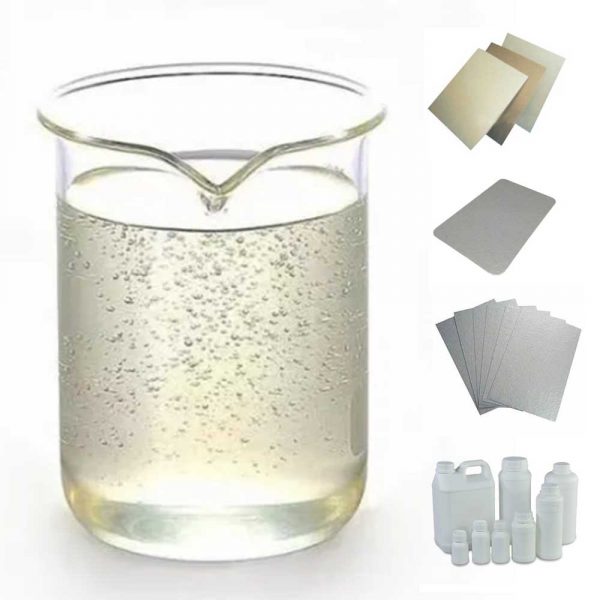
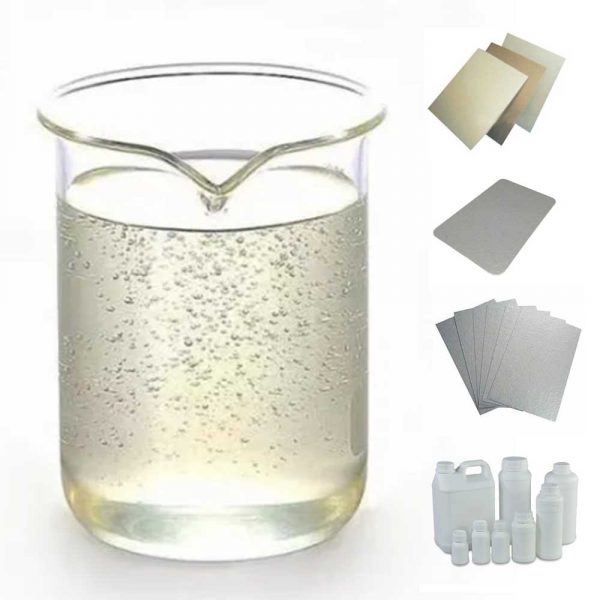
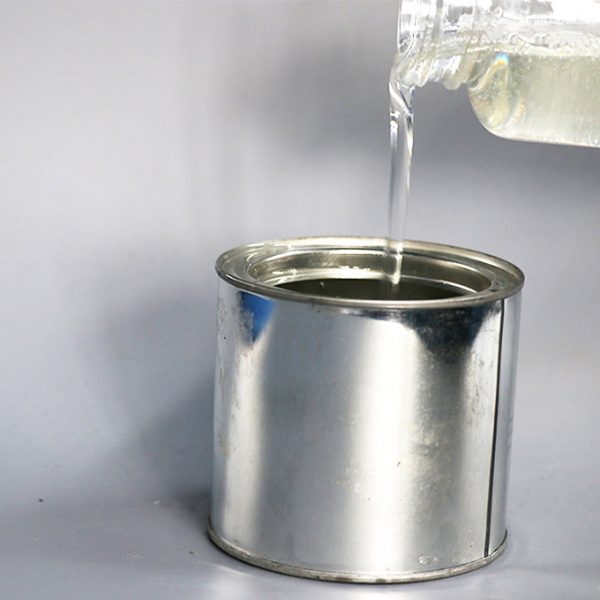
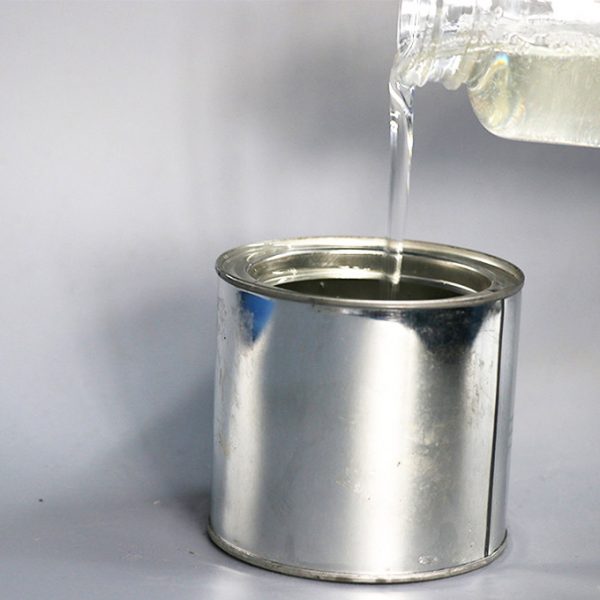
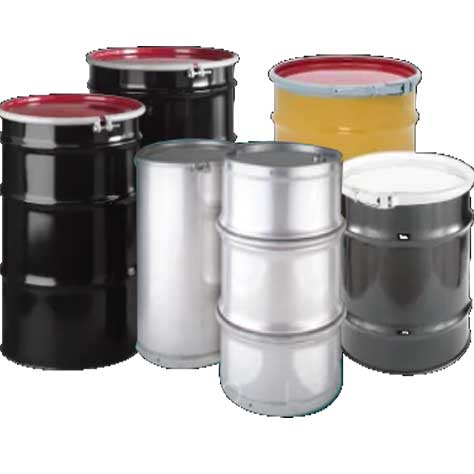

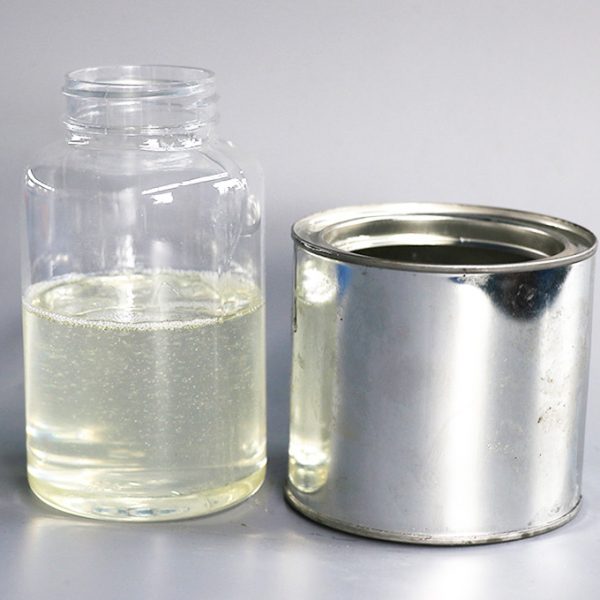
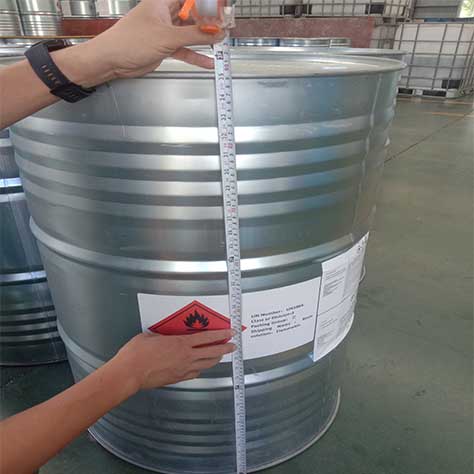
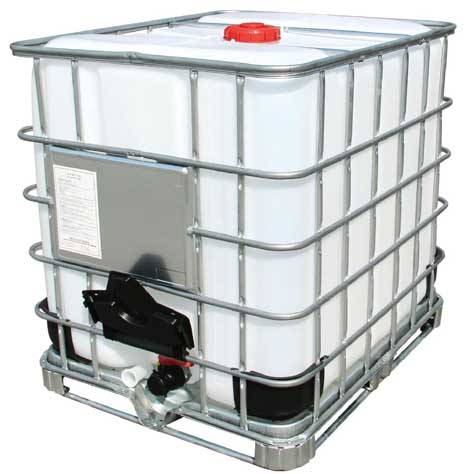
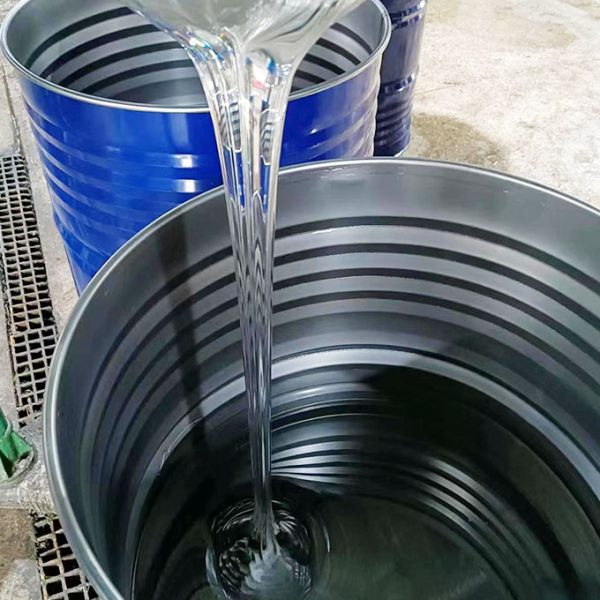
Silicone adhesive (mica tape adhesive)
I.Performance Features
SH922A series organosilicon adhesive is a toluene solution with polysiloxane raw rubber and resin as the base material and then add additives. With high heat resistance, flexibility and good insulation and moisture resistance, suitable for fire-resistant mica tape, pressure-sensitive adhesive tape bonding. Low smoke, good stability, high temperature resistance, no carbon precipitation, weather resistance, moisture resistance, electrical insulation properties.
II.Main technical indicators
Item | Indicator |
Appearance | Colorless or light yellow uniform liquid, allowed to have milky light, no mechanical impurities |
Solid content(150℃,2h,%) | 60±2 |
Density(25℃,g/cm3) | 1.0±0.02 |
viscosity(25℃,cp) | 10000~80000〖1〗 |
Note: 〖1〗Can be customized according to customers’ requirements.
三、Application Notes
- This product is a two-component, can be cured with peroxide BPO or our special curing agent;
- Due to the different factors such as substrate, coating equipment, curing cycle and desired properties, the amount of hardener added is 1.5 to 2.5% of the amount of glue. In order to ensure the best mixing of curing agent and adhesive, first dissolve it completely in solvent and then add it to the glue, stirring and mixing. At the same time, before coating on the machine should be filtered again with a 180 mesh screen to prevent the mixing of mechanical impurities;
- The use of hardeners can speed up curing or allow curing at low temperatures, and can also increase the cohesive strength of the adhesive and improve its adhesion properties to the substrate. Mixed and formulated dispersions can only be used for one to two days, because the curing agent quickly loses its activity in the solvent. Adequate dispersion of the adhesive and curing agent during the mixing process is necessary to ensure the consistency of the finished product’s use;
- ● SH-922A series adhesives can be coated directly with conventional tape coating equipment, and can be further thinned with compatible solvents such as toluene and xylene before coating, and the concentration of the working solution should be about 18-20%, depending on the respective equipment and experience. The use of solvents for coating must be well ventilated, and please observe the safety precautions of the solvent supplier and relevant regulations.
- Surface Vulcanization Cycle: 80-90°C*2min de-solventing to ensure that no solvent is present in the adhesive when it enters the curing zone for vulcanization; 150-170°C*5min to further strengthen the adhesion, cohesive strength and initial tack by heat curing. However, the exact conditions required for complete vulcanization depend on the length, temperature and efficiency of the heating oven, the type of curing agent and the type of substrate used, and tests must be carried out on the equipment to determine the conditions.
- If the equipment and substrate allow for higher curing temperatures, the curing time can be shortened. Increasing the curing temperature allows the cohesive strength of the adhesive to be reached in a shorter period of time compared to curing at lower temperatures.
四、Packaging and storage and transportation
Packed in clean and dry 200kg or 1000L steel drum, sealed with lid. Store at room temperature (0~35℃), the storage period is 6 months (over the period of qualified inspection, can still be used) to prevent direct sunlight, according to the storage and transportation of dangerous goods.