The multi-roll coating unit of the common PVC multifunctional additive JC-880 has three structures
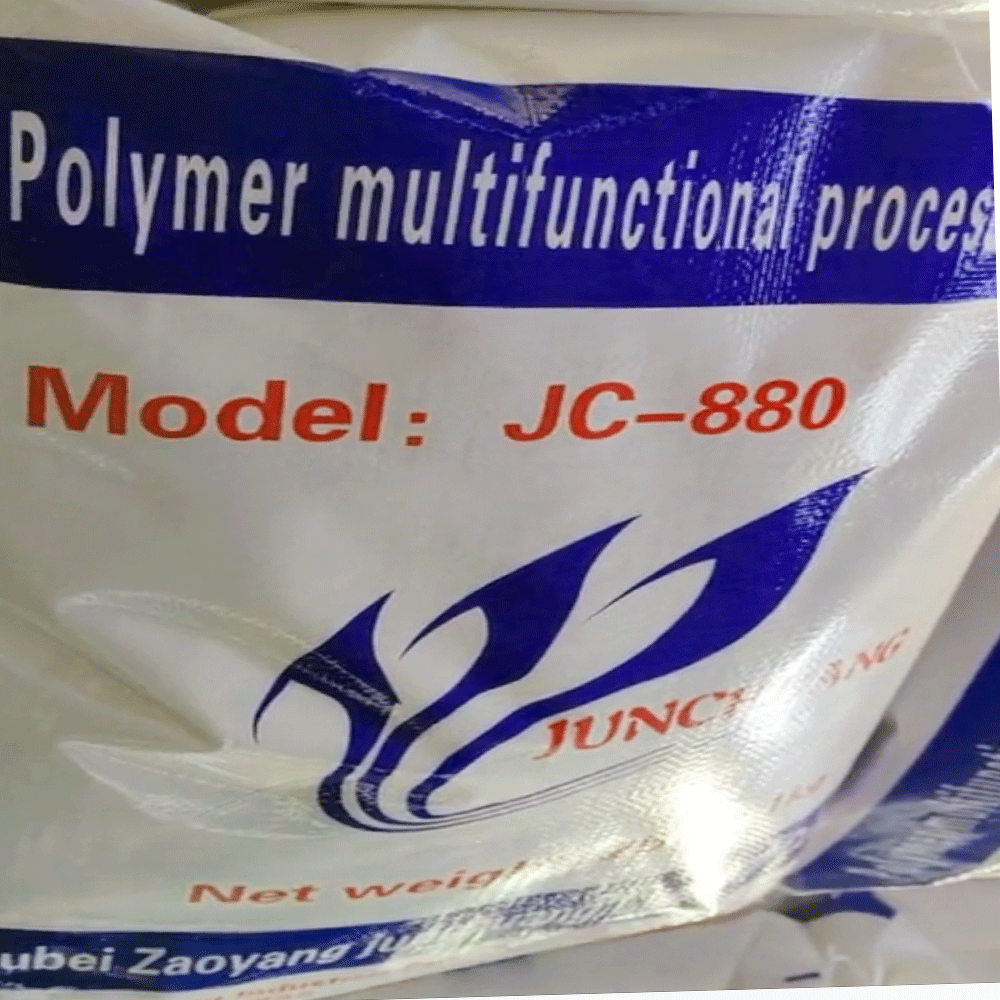
Dry lamination using anilox roller coating, the construction of the initial just coated with good adhesive coating was uneven thickness of concave and convex, need to be in the subsequent film movement and drying process, the adhesive in the drying process before the loss of mobility, through the flow of the adhesive unfolding and gradually become uniform, so the anilox roller coating of the thickness of the adhesive coating layer of the uniformity of the poor, but also difficult to get a very thin layer of coating anilox roller coating; in addition to the anilox roller coating, the amount of coating is mainly determined by the anilox line, once the anilox roller is determined, the amount of coating adjustment range is very limited only by changing the concentration of adhesive to make the amount of coating to get a very limited. In addition, the anilox roller coating, the coating volume is mainly determined by the anilox line of the coating roller, once the anilox roller is determined, the adjustment range of the coating volume is very limited only by changing the concentration of the adhesive, so that the amount of glue can be adjusted appropriately, when the amount of glue for a larger adjustment, the need to replace the anilox roller. Solvent-free composite using multi-roller coating method, with high coating layer flatness coating thickness is easy to adjust and other advantages, is conducive to the realization of the control of the coating, but also to facilitate the production of thinner coatings, saving adhesive, reduce production costs. Compared with the anilox roller coating unit, the structure of the multi-roller coating unit is more complex. There are three kinds of structures in the multi-roll coating unit of JC-880, a common PVC multi-functional additive.
One kind of multi-roller coating unit is a simple structure of four-roller coating device, PVC multi-functional additives JC-880 mostly use this structure. The four-roller coating device consists of four rollers, namely, the rubber roller, steel roller, metering roller, steel roller, coating roller, steel roller, and rubber roller, coating pressure roller. The disadvantage of this design is that the metering roller and coating roller two steel surface in direct contact, the consequences of this one affects the service life of the rollers; secondly, the friction generated by the heat may change the viscosity of the adhesive; thirdly, it is possible to evaporate the adhesive into a mist of particles, thus causing the phenomenon of “evaporation fog” occurs.PVC multi-functional auxiliary JC-880 with four roller coating device. Schematic diagram of the four-roll coating unit for JC-880. Another structure of the multi-roller coating unit is a six-roller coating device, six-roller coating device in the metering roller and transfer rollers between a set of rubber floating rollers and a set of transfer rollers, six-roller coating unit can be part of the binder’s “evaporation fogging” phenomenon. However, the transfer roller steel rod and coating roller steel rod is still in direct contact, there are still some problems in the four-roller coating unit, and the six-roller structure makes the coating unit become more complex, increasing the difficulty of design and manufacturing, increasing manufacturing costs, and therefore is not desirable.PVC multifunctional additives JC-880 with a six-roller coating unit schematic diagram. The third structure of the multi-roller coating unit is the five-roller coating device.
Considering the advantages and disadvantages of the four-roller coating unit and the six-roller coating unit mentioned above, most solvent laminators nowadays use the five-roller coating unit. Five-roller coating unit, is commonly used typical multi-roller coating device. Five-roller coating unit by the rubber roller metering roller floating rubber roller coating roller and coating roller pressure roller is also known as the rubber roller metering roller metering roller called transfer roller floating rubber roller called transfer roller coating roller pressure roller called liner roller, called the difference in the role played in the coating unit, without any substantial impact on the role played in the coating unit, in which the rubber roller metering roller and coating roller for the steel roller, transfer roller coated roller for the rubber rollers. Compared with the four-roller coating unit, due to the addition of a rubber transfer roller between the metering roller and the coating roller, direct contact between the surfaces of the two steel rollers of the metering roller and the coating roller is avoided, which reduces the service life of the two steel rollers of the metering roller and the coating roller, and at the same time avoids heat generated by friction of the surfaces of the two steel rollers, thus avoiding changes in the viscosity of the adhesive due to the frictional heat between the rollers during the production process, resulting in the surface of the rollers being warmed up Avoiding the phenomenon of “vaporization fogging” caused by evaporation of adhesive into mist due to frictional heat. Five-roller coating unit of the metering roller transfer rubber roller coating rollers are independent servo-driven and linear independent adjustment to ensure that the speed of sex. The transfer rubber roller used in the coating unit is an accessory that needs to be replaced frequently due to the different widths of the coated base film.